This is a way to get a shorter
shifter, somewhat reducing the distance of the throws
between shifts. This is not a true short shifter,
which would move the fulcrum (pivot) point of the shifter to
more greatly reduce the travel, but is a cheap way to get a
shorter shaft and the look of a short shifter.
In my case, it was a way to get
rid of the huge gap between the stock shift boot and my
aftermarket shift knob. After the modification, I am
still able to install the stock knob and it looks and acts just like an
unmodified stock shifter.
You can see below how the stock
and aftermarket knobs looked on the shifter before the
modification. Notice the nasty gap with the
aftermarket knob.
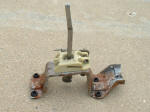
Needed:
Tools:
Something to cut hard
metal with (Dremel, Reciprocating saw, etc.)
Instructions
Step 1:
Remove the Shifter
Assembly
Step 2:
Figure out where you want to cut it. I took as much off
of mine as I could without having to modify the shaft or
boot and be able to use the stock boot with my aftermarket
knob. I just wanted to get rid of the gap between the
aftermarket knob and the stock boot, and I wanted to be able
to revert to the stock knob if needed. For me, this
meant cutting about 19mm off the shaft.
I placed the stock boot and the
aftermarket shift knob on the shifter assembly, and measured
the distance between with a slide caliper.
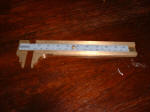
Step 3: Mark your cut. A
sharpie works well. If you're trying to use a knob
like mine, be sure to leave a couple mm for the set screw
cover to slide down a bit so you can tighten/loosen the set
screws. It will leave a little wiggle in the boot when
you're done, but it's a necessary evil. Once I marked
my cut, I checked how much shaft would still be inside the
stock knob. Plenty left.
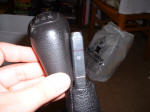
Step 4: Cut. Many people
use a Dremel rotary cutting tool. I used a Dremel at
first, but it was taking too long, and I like overkill, so I
grabbed my Milwaukee Super Sawzall & "the torch" metal
cutting blade. Took care of that really quick (though
it would've been quicker if I had a vice...) After
chopping the tip off, I used the Dremel again with a metal
shaving bit and smoothed out the end. A test fit of
the boot and aftermarket knob proved that it worked very
well. A test fit of the stock knob... not so well.
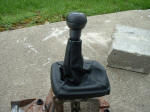
Step 4: Taper. When I
test-fit the stock knob, it refused to go on. Then I
realized that the end I just cut off had a taper on the end
that helped push the clip in the stock knob outward, and my
chopped shaft didn't have the taper. Out came the
Dremel again, and I shaved a taper to it. With the
taper, the stock knob again would go on and click right into
place.
NOTE: the metal shavings that
come off when using a Dremel & metal shaving bit are NASTY
LITTLE METAL SPLINTERS. Have a change of clothes and
some tweezers handy for when you get done, because they will
be everywhere.
